Dial Gauge
It is used as a measuring device to measure the accuracies in alignment, eccentricity of the parts/components.
A dial gauge is like a fine watch. It consists of a graduated dial, pointer, plunger and a clamp. It measures the displacement of its plunger on a circular dial by means of a rotating point.

It works on the rack and pinion principal. The plunger has gear teeth cut on it and when it reciprocates it actuates a pinion attached to the pointer shaft. Thus any movement of the plunger causes a corresponding movement of the main pointer on a graduated dial. In addition to the main pointer the dial gauge has a secondary scale and a small pointer for indicating the number of revolutions made by the main pointer. Zero setting of the main pointer of the dial gauge can be done by rotating the dial face until ‘0’ line coincide with the pointer.

Dial Gauges are one of the most commonly used instruments in all types of automobile related industry.
Bore Gauge/Cylinder Gauge
Bore gauge or cylinder gauge is used to measure hole diameter or internal diameter or bore, ovality and taperness in the IC Engine cylinder.

The bore/cylinder gauge has a dial indicator mounted on a sledge which acts or a guide when the instrument is in use. There are two contact points and a extension roads of varying length as per requirement.
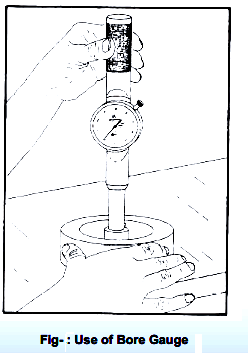
To make a measurement a suitable length rod is fitted and the gauge is inserted in the cylinder where it is carefully traversed up and down in several positions while the movement of dial gauge pointer is observed. In this way we can detect the variations along the bore/internal diameter of engine cylinder. Dial gauge gives fractional reading in 0.001 mm.